Findings from the 2022 State of Industrial Maintenance Report illustrate the importance of effective maintenance planning and scheduling. According to 58% of respondents, the top challenge to improving maintenance is aging equipment.
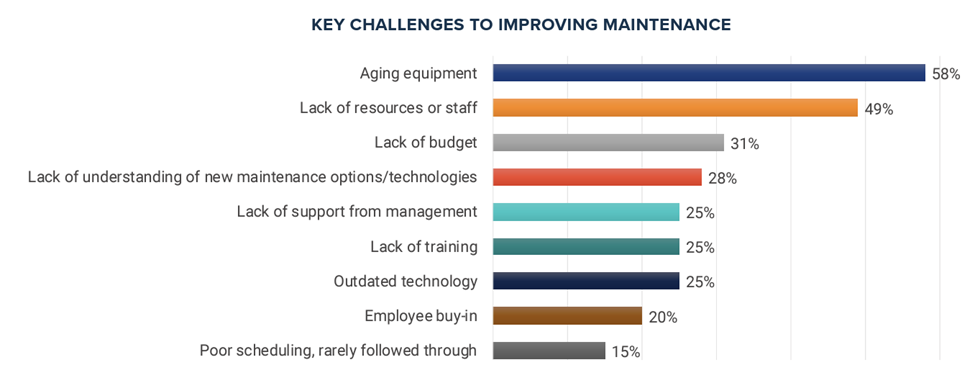
Not only is it a challenge, but 80% cite aging equipment (or machines breaking down and going offline) as the #1 challenge to plant productivity. Not only does equipment downtime affect overall productivity, it will severely impact the supply chain.
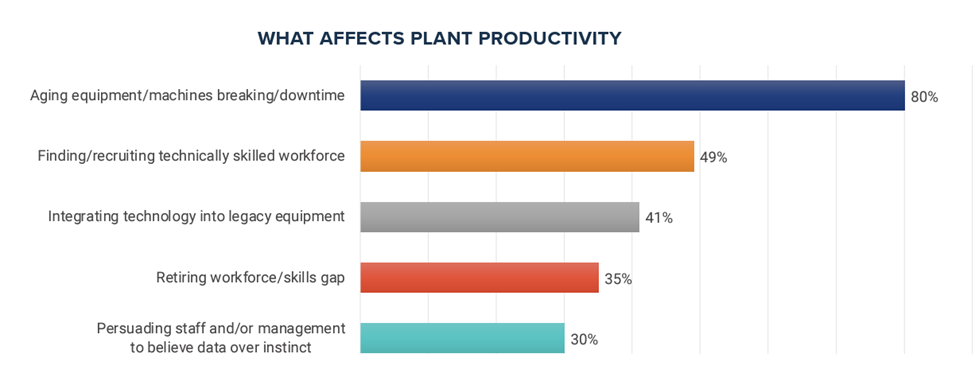
These problems persist despite the average plant spending 33 hours each week on scheduled maintenance. Knowing that a problem will arise is one thing, being prepared to address these problems immediately can be the difference between a positive and negative economic outcome. Applying automation and advanced software to maintenance scheduling will produce immediate value to the enterprise.
Maintenance Scheduling vs. Planning
What. How. When. Who. These are the most important words to a maintenance planner & scheduler.
Why? It’s important to understand where planning ends and scheduling begins. Maintenance planning is the process of figuring out what maintenance work needs to get done and how it should be performed.
Scheduling complements this by establishing when maintenance tasks are to be completed, and by whom. Planning takes a long-term view of plant productivity. Scheduling focuses on more immediate tasks.
While planners spend time analyzing failures and documenting maintenance and repair instructions, schedulers concentrate on adjusting the maintenance schedule to accommodate new, high priority or urgent needs.
Common Maintenance Scheduling Mistakes
As a business grows and plants handle more work, it’s easy to make scheduling mistakes.
1. Scheduling outside of SAP. While many organizations call upon their SAP system for work order data, their maintenance schedulers end up manually downloading work orders from SAP and importing them into spreadsheets to create schedules. A technician’s time is valuable and to minimize disruption to production, schedulers must track down a variety of information.
- Technician’s work schedule, meetings, and vacation
- Parts and materials availability
- Optimal time to service the broken equipment
Once the information is obtained, schedulers manually build a schedule and then go back to SAP to update each work order — a tedious, time-consuming, error-prone process.
2. Scheduling maintenance on the wrong cadence. When maintenance tasks are scheduled too far apart, the risk of breakdowns and equipment failures rises. When these tasks are scheduled too frequently, the result is unnecessary downtime, and wasted technician time. This is an important balancing act and is essential to ensuring equipment and plant uptime.
3. Providing incomplete instructions. When information is wrong or missing, schedulers are unable to prepare technicians with the right details to efficiently perform the scheduled task. For example, technicians might show up at a job without the right spare part or tool. Or the scheduling manager may have inadvertently omitted guidelines, manuals, or checklists from the work order — an easy oversight when preparing paper-based work orders. Without the needed resources to complete the task, technicians are forced to leave the worksite — or push the work order to another day.
4. Failing to communicate scheduling changes. When in the field, technicians need to be kept up to date on scheduling changes. However, a busy scheduler, juggling multiple technicians and maintenance requests, it is challenging to communicate change in a timely manner. Communication breakdowns can lead to conflicts and delays in performing maintenance tasks.
5. Overlooking equipment-specific maintenance recommendations. All large machinery and equipment are not valued equally. Some is more critical than others, requiring maintenance based on various indicators like vibration, temperature, or fluid levels. Some maintenance schedules don’t prioritize maintenance based on equipment criticality, while others don’t incorporate condition-based maintenance.
6. Keeping inadequate records. Many preventive maintenance tasks are repeated, and maintaining accurate documentation within SAP, of the tasks performed, is critical to long-term success. Keeping detailed records of maintenance activities, breakdowns, and repairs, allow maintenance planners to optimize the frequency of PMs, time required and work instructions. More accurate PM’s help the scheduler plan the right amount of time for the work, creating trust in the work schedules, and more efficient use of a technicians’ time. Detailed records also create institutional knowledge for schedulers to get the most knowledgeable technician to the job quickly.
7. Failing to leverage technology and modernize. In today’s world, every organization must harness technology to better enable their employees and operations. Manual processes and legacy software can lead to many of the issues discussed above. Continuing today, many schedulers and technicians lack an understanding of new maintenance options and technologies at their facility. Outdated technology is often cited as a barrier to improvement. Lack of growth hinders the creation of a world-class maintenance organization and inhibits value creation by the maintenance organization. Value that would benefit the entire enterprise.
Optimize Maintenance Scheduling With the Right Software
With the right tools, maintenance planners and schedulers can work more efficiently and help ensure equipment uptime powering organization-wide productivity. For maintenance schedulers, the right software makes all the difference.
Rather than sift through downloaded transactions from SAP in a spreadsheet, schedulers can use tools to automatically sort data and create views for quick decision-making. In the process, schedulers will save hours every week. Imagine an 80% reduction in time spent on scheduling.*
The right scheduling software can track the skills and availability of maintenance staff and automatically create a baseline schedule based on that information. Advanced software comes with different UI options, such as a Gantt chart to check dependencies and facilitate schedule refinement. Even better, some accommodate unique and changing needs by allowing maintenance schedulers to add custom rules (such as equipment criticality) to the scheduling automation for even more efficiency.
With 23+ years’ experience with SAP, asset management, and industrial maintenance solutions, Sigga offers a Planning and Scheduling solution that seamlessly integrates with SAP and improves the maintenance organization’s interaction with SAP.
Key functionalities include:
• Detailed databases. Effectively plan and schedule work orders with data to augment work order details from SAP, including technician skills, technician availability beyond work shift, parts inventory and turnaround time from vendors, equipment availability agreements with production and more.
• Automation. Sigga’s advanced scheduling algorithm creates schedules from SAP and detailed databases, allowing schedulers to simply evaluate the result, align with stakeholders, and finalize the schedule. Drag and drop features puts ease of use in the palm of a scheduler’s hands.
• Mass updates to SAP. Schedulers can easily adjust and load maintenance schedules into SAP, eliminating the need to update each work order manually.
• Dispatch. With Sigga’s integrated Mobile Maintenance Solution, schedulers can simply dispatch work orders for execution and ensure a fully digital, end-to-end maintenance process.
See how our Planning and Scheduling solution has been specifically designed to complement your SAP PM investment.